
This tool is also called a cause and effect diagram or an Ishikawa diagram. A fishbone diagram is perhaps the easiest tool in the family of cause-and-effect diagrams that engineers and scientists use in unearthing factors that lead to. Ishikawa gave this quality circle a toolbox for quality management – it still contains the Ishikawa diagram today. This type of analysis enables you to discover the root cause of a problem. A key element of the concept is therefore the quality circle, in which a group of employees works on the quality management of a company in a focused manner. Ishikawa diagrams can be used as a tool in the following scenarios. It is a functional tool to break down all contributing factors to the problem or event in a hierarchical manner.
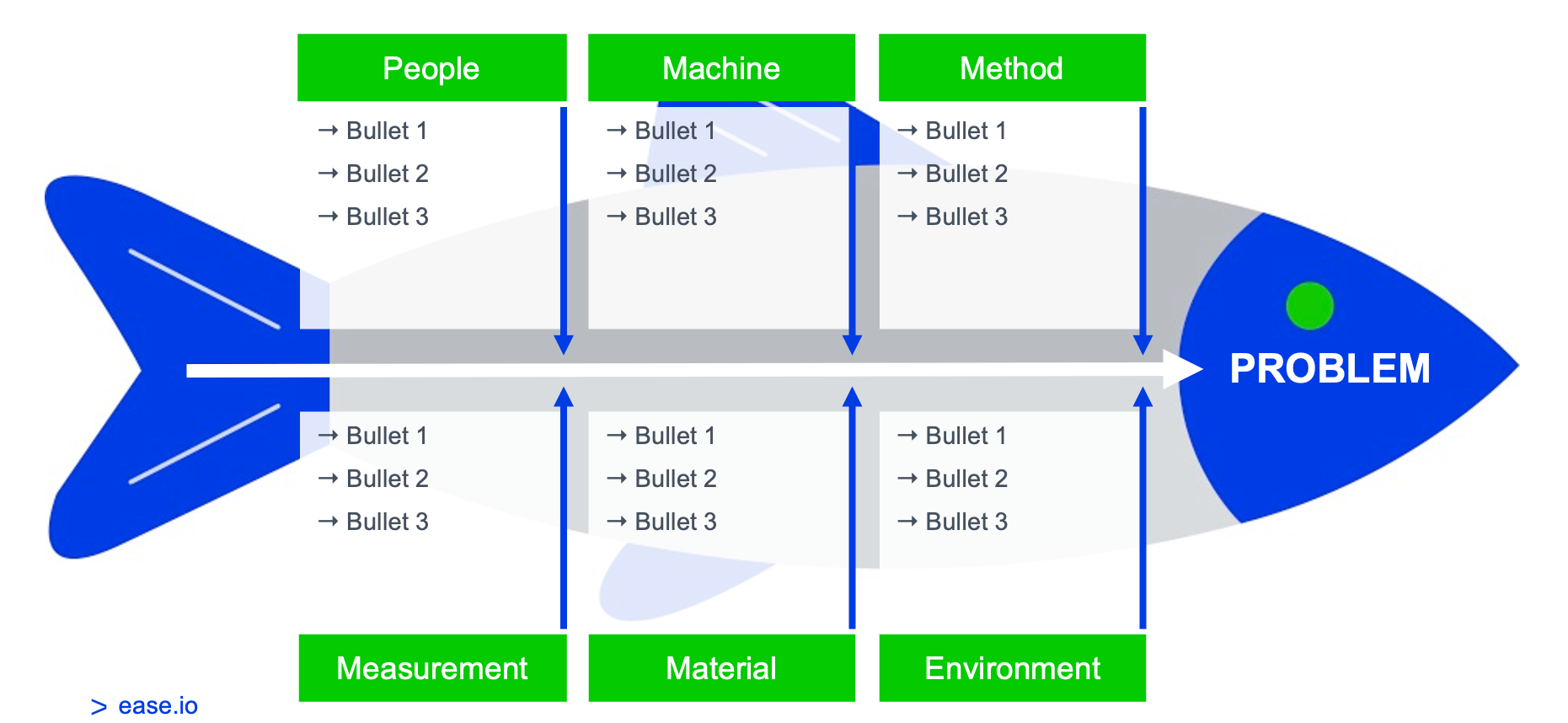
Managers mostly use the Ishikawa diagram or the cause and effect diagram as a tool in finding out the deviations that are necessary to detect for business expansion. However, it has proved its talent now and is being used for many versatile purposes. Ishikawa or fishbone diagram is one such diagram to detect the causes and effects of various imperfections, failures, or defects in the business. This is based on the idea of Total Quality Management (TQM). Ishikawa diagram was conceived as a tool to aid in problem-solving.

These defects or imperfections are known as variables that affect the quality of the. The main purpose of this tool is to minimize any defects or imperfections that may adversely impact the final output. The Ishikawa Diagram, also known as Cause and Effect Diagram and also as Fishbone Diagram is one of the 7 tools that make up the quality. Ishikawa diagram example Through them, the employees involved in the task are able to analyze all the factors involved in a given process, thus raising the main bottlenecks and points to. He developed an employee-oriented concept for cross-divisional quality work – the concept of Company-Wide Quality Control (CWQC). A fishbone diagram is also known as a cause-and-effect diagram because it studies the root causes of a problem. The Ishikawa Diagram is a visual tool that helps in identifying the main causes of a problem, and is often implemented in process quality control processes. In Japan, Ishikawa is regarded as a pioneer in the field of quality: the end of World War II and the destroyed industry led to a quality offensive in the 1950s, in which Ishikawa played a major role, building on the work of William Edwards Deming, Joseph M.
Ishikawa diagram tool professional#
During his professional career, he taught at the University of Tokyo, among other places, was a member of the Japanese Union of Scientists and Engineers from 1949 and worked in its research group for quality assurance.
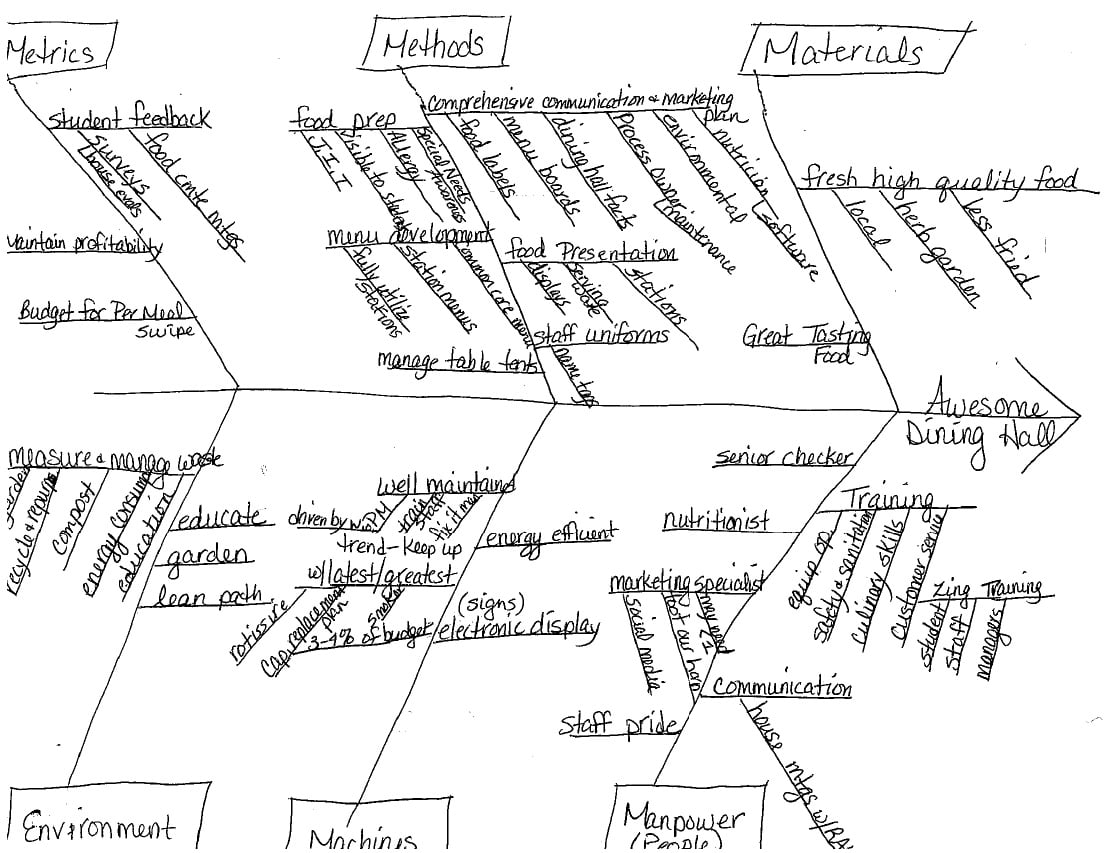
Kaoru Ishikawa (1915 – 1989) was a Japanese chemist.
